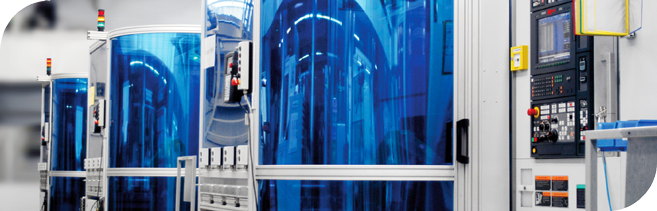
Technology mix in perfection –
just one of our strengths
With around 100 CNC processing machines we primarily manufacture midsize series up to fully automated large scales with daily volumes of more than 25.000 pieces.
Our particular strengths are complex turning-, drilling-, grinding and milling operations of all kinds of metallic materials with narrow tolerances up to the IT6 range. We manufacture our components in several value added stages with appropriate deburring (i.a. ECM).
Since the cleanliness of our products plays an increasingly important role for our customers, we have also focused on provision and conformity with strict residual dirt specifications. We therefore, among other things, have the most advanced washing technology (also with high pressure) and appropriate equipment to determine residual dirt.
Our technologies used for your products
Turning & Milling
- free-cutting steels, case-hardening steels, tempering steels, high-grade stainless steels, light metal alloys, powder metal materials
Primary materials:
- bar material, saw cuts, cold and hot forged parts, prototype parts, profiled materials, prehardened steels up to 42 HRC
Geometries:
- Turning from diameter 6 mm to 200 mm (vertically and horizontally), Tipp lengths up to about 200 mm
- CNC-lathes from single spindle to multispindle technology
- Milling of cubic parts up to about 200mm x 200 x 200 mm
- CNC-milling machines with 3 - 5 axes
Accuracies:
- IT6 for length dimensions and diameters
- Shape- and positional tolerances up to 10µm
- Shape- and turning parts partially up to 5µm
Piece weights:
- 2g – 12,0 kg
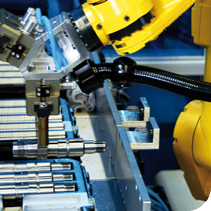
Deep hole drilling
- Free-cutting steels, tempering steels, light metals
Geometries:
- Clamping diameter 10 – 30 mm
- Bore diameter 3 – 10 mm
- Drilling depth up to 350 mm
Accuracies:
- Concentricity accuracies from 0,05 – 0,1 mm/100 length/li>
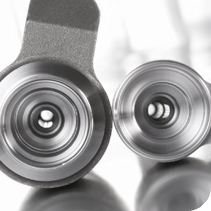
Grinding
- Cylindrical-, excentric-, polygon and profile grinding
Geometries:
- Diameter up to a maximum of 200 mm
- Length up to a maximum of 500 mm
Accuracies:
- Diameter IT5
- RZ-value up to 2 µm
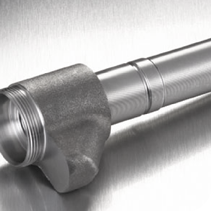
Deburring
- Electrochemical deburring (ECM)
- Pulse-ECM
- High-pressure deburring (HD)
- Barrel finishing
- Thermal deburring (TEM)
- Integrated in the manufacturing process: brushing, high-pressure rinsing
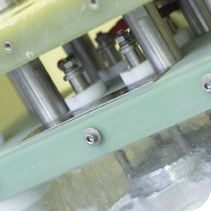
Cleaning
- Aqueous immersion bath systems with multilevel ultrasonic- and flood washing
- Aqueous chamber washing systems with ultrasonic washing and pressure flooding
- High-pressure washing systems (up to 700 bar)
Cleanliness requirements:
- Particle size: ≤ 200µm
- Residual dirt ≤ 0,5 mg / piece
- High-pressure washing systems (up to 700 bar)
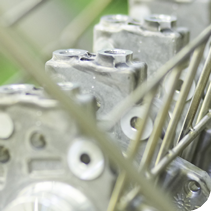
At our plant for the residual dirt analysis the evaluation of technical cleanliness is done by particle size (pattern perception) and particle weight (weigh out), according to VDA19.